HOW HILTI MAKES THE PERMANENT FORMWORK PROCESS FASTER
Permanent formwork applications for building construction
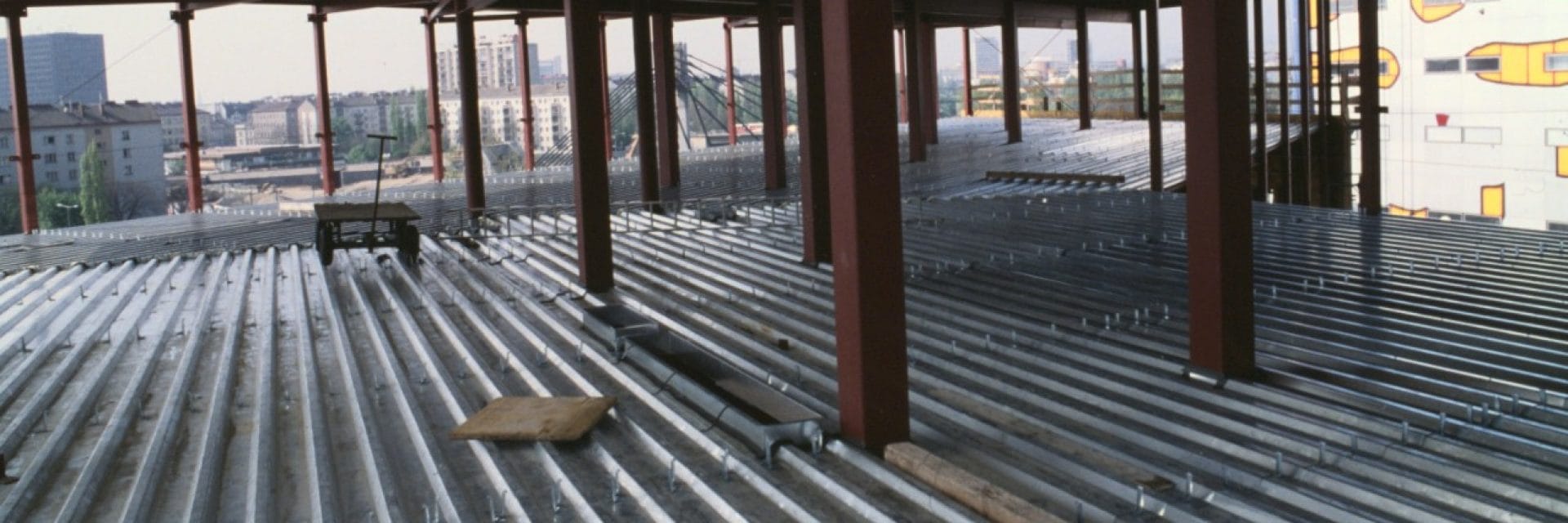
We have a range of products that are perfectly tailored to permanent formwork systems.
Companies such as Dincel, AFS and Ritek are leading the permanent formwork charge, and as a result we are seeing a rapid increase in construction speed. In the past, formwork has been mostly associated with putting down horizontal slabs, but new technologies and methodologies have made it possible to pour vertically and create walls. Perhaps most importantly, the process has also been embraced by architects, so we can all expect to see a lot more permanent formwork applications over the coming years.
With all of these factors in mind, we're going to take a closer look at the process, as well as how Hilti's product range can make it easier, quicker and better.
Share via: